To provide a better understanding of build-to-print in general and the breadth of our offerings, as well as how our thin-film technology can benefit your applications, we’ve put together a Build-to-Print Basics series. Part 3 provides an overview of the two broad types of applications where build-to-print designs using thin-film technology offer more reliable options versus off-the-shelf solutions.
As discussed in part 1 of this series, custom thin-film structures can be manufactured to meet the most precise requirements, from simple-patterned submounts to highly complex circuits. In general, if you are building a circuit with size, weight, and power (SWaP) concerns, thin film is a good choice because it can reduce complexity and size while maximizing performance. While there are quite a few applications where thin film is a good fit, let’s explore two of the main application types where a build-to-print approach with thin-film technology is an excellent option – heatsinks and standoffs and integrated passive devices.
Heatsinks and Standoffs
When designing a heatsink or standoff, considering the thermal and electrical properties is extremely important. As the applications these devices are used in are becoming more compact, yet ever more complex, it is difficult for off-the-shelf heatsinks and standoffs to meet the requirements of many electronic component manufacturers. Thus, many manufacturers are looking for suppliers that can work with them to develop a build-to-print option instead.
While the common materials we use for all types of build-to-print applications were discussed in part 2 of this series, for these components specifically we recommend using Aluminum Nitrides (AlNs) because of their excellent thermal properties. AINs are unique because they have both high thermal conductivity and strong electrical resistance, which is unlike most electrically insulative materials that are also thermally insulative. As a result, AlN allows electrical systems to dissipate heat quickly to maintain maximum efficiency.
At Knowles Precision Devices, we specialize not only in knowing the best materials to use for your specific application, we are also experts in knowing how to make precise electrical connections in these types of sensitive applications with high-density interconnects. For example, instead of using a standard PCB, which likely cannot reliably withstand the high operating temperatures of these devices and does not allow for control of finer features, we take an approach similar to semiconductor companies and use lithography to make these precise connections.
More specifically, looking at one specialized version of a heatsink, the laser diode submount, this component has incredibly high thermal requirements. When arranged in high densities, heat dissipation for laser diodes becomes even more critical, which makes our thin-film technology a good option. In these high-density components, a long wire bond connection will make the bond worse electrically. Therefore, we use Alumina mounting shorts to create short bonds. This approach allows for placement of a wire bond anywhere in the circuit and replaces the need for gold terminations on the substrate (Figure 1).
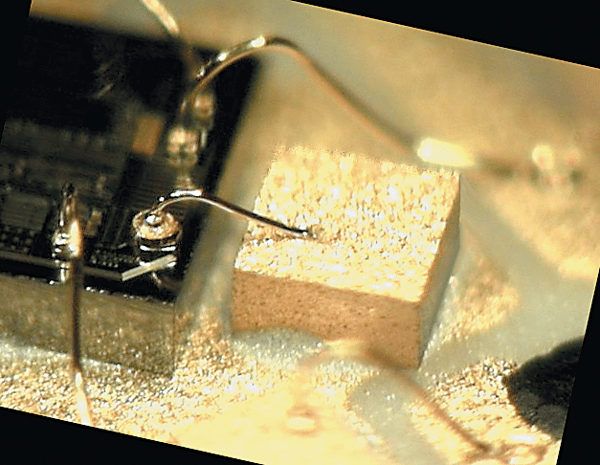
Figure 1. An example of a mounting short used to create a short bond on a laser diode submount.
Integrated Passive Devices
Integrated passive devices (IPDs) have been around in some form since the 1960s as a way to reduce the total number of assembly steps in manufacturing a circuit. This approach has gained popularity over the years since it reduces overall manufacturing costs and addresses various SWaP concerns.
Ranging from simple to complex, IPDs can combine a variety of circuit building blocks such as conductors, resistors, plated vias, selective high-conductivity traces, integrated resistors, filled vias, bridges, and transmission line structures, into one device. However, if not done correctly, condensing multiple passive components into a small device can lead to a number of issues.
This is why a build-to-print approach is a great strategy for developing an IPD. Not to pick on the poor old PCB again, but PCBs take up a ton of space relatively. Instead, you can build an IPD with thin film to safely place several connections close together. With this approach, in the end device, there is just one component being placed instead of dozens of capacitors and resistors, which is a huge space and time saver.
Typical use cases for IPDs include the following:
- Custom resistor capacitor networks – If you can draw it on a napkin, we can make it
- Lange couplers and power combiners
- EMI filters
- High-frequency filters
- Microwave integrated circuits
- Bias decoupling and filtering
- Lumped element impedance matching networks
- PA stabilizations
- Impedance matching and power combining networks
Figure 2. A sampling of IPDs, including a spiral inductor, interposer, and a power divider, that we are capable of making.
If You Can Draw It, We Can Make it
From a single capacitor and resistor to a super complex IPD, if you can draw it, and it’s within our menu of capabilities, our build-to-print team can make it. Additionally, since we specialize in working with military and aerospace organizations, we are incredibly familiar with making components that are compact and reliable, even in incredibly harsh environments.
Finally, we know how to put thin film down using a proven process that makes things work the way they are supposed to. We will talk about this process more in the next post in this series. In the meantime, you can also check out our Build-to-Print page to learn more about the technical aspects of our offerings or download the comprehensive Build-to-Print Ebook today!